This article has been adapted from a recently published visionary paper in Photovoltaics International Magazine.
What is Industry 4.0
Industry 4.0 is a term initially coined in Germany in 2011. Since then, it has become a bit of a catch-all for everything that has to do with advanced industrial digitization and process automation. In this article, we interpret Industry 4.0 as the transfer at a point in time of (significant quantities of) data – generated manually or automatically – between stakeholders across the production value chain in an automated and dynamic way. This means that relevant parameters are being monitored and exchanged from the design stage to the installation stage. Moreover, as soon as something changes, the data are automatically updated, and (artificial intelligence – AI) algorithms consider all the interlinked processes and consequences as well.
To illustrate the above concept as a hypothetical and oversimplified scenario for the PV sector, consider an architect designing a building requiring a specific set of building-integrated PV (BIPV) modules in terms of size and energy capacity. All relevant information is stored in a digital file, which is the central frame of reference for everyone downstream of the production and installation chains. Imagine that, during construction, the architect observes a deviation from the building plans, requiring adjustments to the BIPV modules. By simply entering this new information in the digital file, the BIPV manufacturer and its suppliers receive an automatic update of the new specifications.
Or, vice versa, if in-line tests during PV production show a deviation from the electrical parameters, the architect gets an automatic alert, along with a suggestion from an AI application on how to compensate for this in the building information management (BIM). Possible suggestions could be to request a new production run, or to make adjustments elsewhere in the building design.
As will be illustrated throughout this article, Industry 4.0 is a multifaceted topic. The scenario above is therefore merely used to underline the fact that the strategy goes beyond on-site automation. Furthermore, Industry 4.0 is more of a transition than an actual state or end goal: in an evolutionary way, the PV sector – as in the case of all the other sectors – will gradually move to Industry 4.0. It makes little or no sense to try to define whether ‘you are already there’. For us, there are two important indicators for the value and maturity of Industry 4.0 in any given sector: first, the observation that it generates new revenue models; and, second (which is strongly linked to the first index), the changes seen in the value chain – mergers, new players entering or existing ones becoming obsolete, etc.
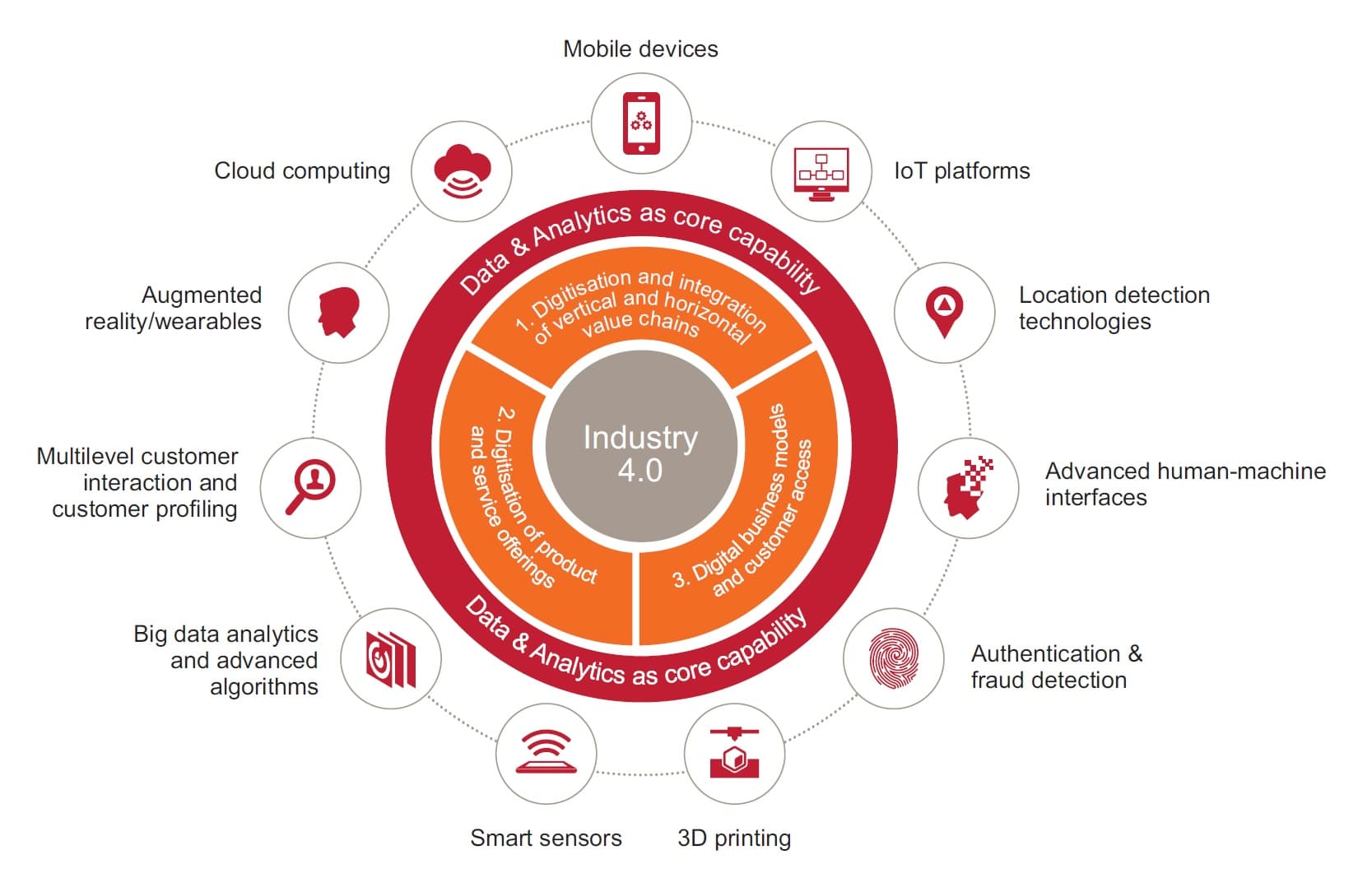
Industry 4.0 in all its facets according to a study “Industry 4.0: hype or reality?” by PWC and FlandersMake (©PWC)
Opportunity for European PV sector
The success of today’s PV industry is based on scaling up manufacturing capacity and on maximal standardization of current PV products to ensure maximal cost reduction of PV products for the PV power plant sector. This is a challenge in which the Asian players have demonstrated superior performance. The challenge in relation to the manufacturing of PV products for new markets such as BIPV is fundamentally different and requires a close link with local market players and customers. This opens up a real opportunity for new players in Europe, where extensive renovation of the existing building stock in an urban context will be necessary in order to achieve the goals set by the European Directive on near-zero-energy buildings (NZEB) and local energy communities. In addition, the current practice of constructing near-zero-energy houses will be insufficient to reach the CO2-emission reduction targets for 2050. We see a need for further developing the concept of ‘plus-energy houses’, which produce more energy than they use.
Buildings have relatively long life cycles before they need to be replaced, so it will be essential to speed up the development of the required technologies. For ease of argument, our initial discussion of the transition of the PV sector to Industry 4.0 will focus on building applications, since this a rapidly growing market, specifically in the EU; other application sectors will be explored in a later section. The scenarios described here will be built around crystalline PV, accounting for 95% of the global PV market. In addition, module manufacturers will be given a central role in the build-up of this story. In our opinion, they will assume a central role in the transition to Industry 4.0, which might allow them to reclaim a European stake in the global PV value chain.
Let’s examine the variety of stakeholders who will be involved and how to make them part of the transition.
Software makes the architect an energy expert
As mentioned, building architects are likely to be the ones furthest upstream in the chain. Typically, they mostly focus on a building’s function and aesthetics; not to be neglected, of course, is the fact that they must consider legislative parameters regarding the energy performance of the buildings they design.
In an Industry 4.0 scenario, it will become increasingly possible to design buildings around their energy properties; probably the first example of such an approach is the Barcelona Forum, founded in 2004. Thanks to Industry 4.0, architects will have software at their disposal, assisting them in optimizing their designs in respect of the desired energy efficiency, and in translating the final design into CAD files (or something equivalent) to be used for module design, assembly and installation. Once such solutions find their way into the PV production chain, this will immediately broaden the architect’s scope and skillset and will create the first link with what happens downstream. Such assisted design in the building domain could lower the acceptance barrier to BIPV adaptation in the broader architect community. Architects could truly consider BIPV as ‘smart or special glass’, and design assistance could invisibly consider the electrical part of the design.
Module assembly builds on new technologies and partnerships
Now that the module supplier knows what to build, they can use the digital files to order their parts and plan their production runs, or even better still, their AI software will have already done all that for them. In this context, they will upgrade their partnerships with, for example, their glass manufacturer and their suppliers of cells, interconnections and lamination materials. At the cell level, no extreme customization is seen to be happening. It is our current belief that cells might in the foreseeable future remain standardized products to be produced and ordered in large quantities. And, although the variety of shapes, colors and sizes might become increasingly diverse, we feel that the catalogue of available cells will remain manageable and that customization will initially occur at the module level.
Innovations in interconnect- and lamination technologies, such as this fabric-based foil (left), could ease customization and integration (right) in an Industry 4.0 scenario.
The possibility of working with a woven fabric-based foil, which functions as the lamination foil and has integrated interconnections, is currently being examined at imec. Once in the production stage, this foil could be custom designed in the shape of the glass and module, significantly increasing the ease of customization. This means, however, that players from the textile industry will be introduced into the equation as new stakeholders. As a consequence, the digital file that is at the basis of the Industry 4.0 scenario might also need to include the necessary parameters for weaving, etc. Needless to say, a crucial role and a lot of opportunities for software developers are envisaged along this entire journey.
After all parts have been ordered and delivered, the assembly process can take place. At present, for custom-module designs, a lot of manual interventions are still needed; this is in contrast to standard cell and module manufacturing, in which highly automated production technologies are already mainstream.
Once automated technologies have been implemented in custom-module manufacturing, they will allow (AI-supported) optimized process-flow management and execution, for example by smartly combining and planning batches in the light of the custom settings to be altered in the assembly line.
Furthermore, automation will significantly improve quality. Cracks and other errors introduced by the handling of strings of cells, for example, can be avoided; similarly, better controlled and homogeneous pulling forces exerted while applying the lamination foils, etc. will minimize breakages, etc. Technically, there are no significant restrictions in automating customized module assembly.
At the moment, imec is ramping up its TWILL BIPV R&D project, which looks into precisely these aspects. Central to the project will be a 12-metre pilot line for the automated assembly of customized PV modules. However, because of the low production volumes, it is not yet economically viable for module manufacturers to proceed in this direction. A transition towards fully automated assembly will become justified when one or more launching customers emerge; for example, a global project developer looking for complete design freedom might require a large number of customized PV modules.
Large-scale projects can kick-off the market for customized BIPV and thereby justify the transition to automated production and assembly. Left: City of Music, Paris, Shigeru Ban architects, BIPV by ISSOL | Middle: French Ministry of Defense, Paris, ANMA architects, BIPV by ISSOL (©Agence Nicolas Michelin & Associes) |Right: Finance Tower, Liège BE, Jaspers Eyers architects, BIPV by ISSOL ©P.Andrianopoli (Pictures: Courtesy of ISSOL).
It should be noted that in view of the specific technological evolutions related to BIPV and printed electronics (e.g. organic PV – OPV), the module assembly scenario depicted above will of course have different consequences. Nevertheless, the overall outcome of this step will largely be the same: at the end of the line there will be PV modules ready to be transported to the construction site.
Robots rule the construction site
Moving on now to the construction site, one again encounters several relevant stakeholders. The shipment of large glass panels to the site within a tight framework has its own challenges, with manufacturing- and traffic-integrated planning being essential. First, the construction workers, such as builders and electricians, on site: radical changes as a consequence of Industry 4.0 might be seen at this level too. Will the electrician still be responsible for the electrical layout, or will the layout have already been generated and provided to him by one of the software modules being used in the building design phase? And will modules be installed manually, or will module installation be fully automated by robotic cranes that are preprogrammed to do the job?
Second, at this point all the peripheral components, such as inverters and batteries, will need to be installed as well. In an Industry 4.0 scenario, these too will have been custom ordered to match the system requirements. Furthermore, technical evolutions in these domains will allow modular solutions that, during operational lifetime, can also flexibly adapt to the building’s real-time energy demand and supply. Finally, there is the maintenance aspect to be considered. Since downstream in the production chain Industry 4.0 ensures the logging of relevant data, these become an important input for the BIM. Aspects such as predictive maintenance and performance analysis will all become more efficient thanks to the data that will readily be available.
Data management outsourced to a trusted intermediary
Data is the main currency in any Industry 4.0 scenario; associated with this data are the aspects of ownership and security. In order to make Industry 4.0 a reality, stakeholders who are currently competitors with each other will be obligated to share data: for example, between equipment manufacturers the sharing of data relating to production runs almost implicitly means that information about the specific machine specifications or settings are included or can be extracted. We envisage that a new stakeholder will emerge who will hold an intermediate role in order to anonymize the data and manage the information flows extracted from it; legislative powers will also need to cater for this.
In the same way that data cannot be treated as an isolated entity, the building’s energy forms part of a larger grid. At some point, Industry 4.0 scenarios will also have to look into the more holistic challenges and opportunities associated with this. On top of the localized energy optimization being performed in the building design phase (e.g. accounting for shadows), grid optimization will also be necessary. The upshot of all this is that protocols will need to be put in place to facilitate smart communication between multiple BIMs and grid management systems.
Break through the linear production hierarchy
With regard to value-chain optimization in PV module assembly, it could be argued that there are quite a few similarities with the automotive industry. For decades, that sector has been adopting a highly integrated approach, involving car manufacturers, their tier suppliers and their distribution and dealer network to the customer.
Before the PV sector starts mimicking those elements, however, one must be aware that this industry too is in a state of constant evolution. A recent presentation at the imec technology forum by Thomas Müller, Executive Vice President at Audi, illustrated the need to break through the rather linear hierarchy of tiers 1–4 suppliers and the collaborations and partnerships that come with it. His argument was that car manufacturers need to interact more closely and directly with semiconductor companies. These companies are now typically in tier 4, and so are rarely, if ever, on the agenda of the manufacturer. Supporting his argument, Müller gave the example of an electronics component used in door handles, which – thanks to such direct interactions – was reduced to just 20% of its original size, allowing significantly increased design freedom for the car designer. As in the case of the car industry, the PV sector will also need to restructure and strengthen its partnerships with these and other sectors.
Living labs as essential test beds
To gain a better understanding of these and other facets of the Industry 4.0 transition, imec is currently involved in several ‘living labs’ in Flanders, almost all of which are in close collaboration with Flanders Make, the strategic research centre for the manufacturing industry. The work at these living labs will also involve exploring aspects such as:
- Connectivity (tags, drones and other technologies for indoor localization and process optimization),
- Co-bot operations (e.g. looking for an optimum in the operator’s cognitive load during their cooperation with industrial robots).
- Energy (e.g. how to find a balance between the massive amounts of data that can be generated and the increasing energy demand of large data centers).
- Computing (e.g. clever selection of data and distribution over edge versus cloud computing).
- Challenges for smart maintenance and circular economy (e.g. recycling, reuse and other end-of-life scenarios).
Living lab settings such as these will become increasingly important in also prototyping the new collaboration and partnership structures that come hand in hand with the Industry 4.0 transition.
They will also be useful for detecting and filtering out the directions that not only are sustainable but also bring economic value. To give just one example in the context of a circular economy, consider Atlas Copco, a world-leading provider of compressors, vacuum solutions, air treatment systems, etc.; this company has already for many years reclaimed used equipment from its clients and sells it on (after revision) to another client who might not necessarily be looking for state-of-the-art products. Why not introduce a similar business model into PV installation? Imec, jointly with the H2020 CIRCUSOL project partners, is exploring technical and business aspects of the circular economy in PV and batteries.
PV breakthrough to new markets
New business models, partnerships and progression in the construction sector are just some of the advantages Industry 4.0 can bring to the PV industry. It is also felt that Industry 4.0 can mean a definite breakthrough for PV into new markets, such as aviation, automotive and marine; there is an increasing tendency for all of these markets to shift to electric-powered vehicles. However, for PV to fulfill its potential in these markets, some catching up needs to be done – first, at the PV-powered charging station level, and, second, at the vehicle-integration level itself. One of the main reasons why PV is trailing behind is its limitations regarding customization and integration. If, as argued, Industry 4.0 were to drastically increase the PV sector’s capabilities with regard to these two aspects, one might finally see PV taking off in these new sectors as well, not to mention the possibilities created through the abundance of sensors for Internet of Things (IoT) and Industry 4.0 applications in all sectors imaginable. It is hard to believe that all these sensors will be battery powered, but not difficult to predict that they will also probably require advanced customization of PV modules in order for them to play a role.
Conclusion: wisely evolve to industry 4.0
In summary, we have shown that the transition to Industry 4.0 is an evolution that, for the PV industry, brings an almost equal number of opportunities as it brings challenges. Grasping the entire complexity is an almost impossible mission, let alone trying to predict the sequence of events that will lead PV into Industry 4.0. What is possible, however, is to identify some of the guiding principles that one should keep in mind.
One of these principles is that the choices to be made should always be weighed against the value that they will bring; this is to be accomplished within a framework comprising economic parameters (will the choice bring the company more, or new, business?) and sustainability ones (will the choice lead to a healthy planet with healthy people?). In support of the choices, a rethink of some of the fundamentals behind the partnerships will be necessary, and living lab environments could assist in this process.
Moreover, if appropriate action is taken, Industry 4.0 could also spark a revival of the European PV industry, as it is likely that globally our ecosystem will be the best placed to tackle this holistic challenge.
Want to know more?
- “Industry 4.0: hype or reality?” (pdf), a 2017 Industry 4.0 Survey by PWC and Flanders Make.
- Homepage of the EU-funded CIRCUSOL project: circular business models for the solar power industry.
- TWILL-BIPV: improve the aesthetics and performance of PV modules by developing an innovative cell interconnection technology for bifacial solar cells.
- Homepage of EnergyVille: a collaboration between imec and the Flemish research partners KU Leuven, VITO and UHasselt in the field of sustainable energy and intelligent energy systems.
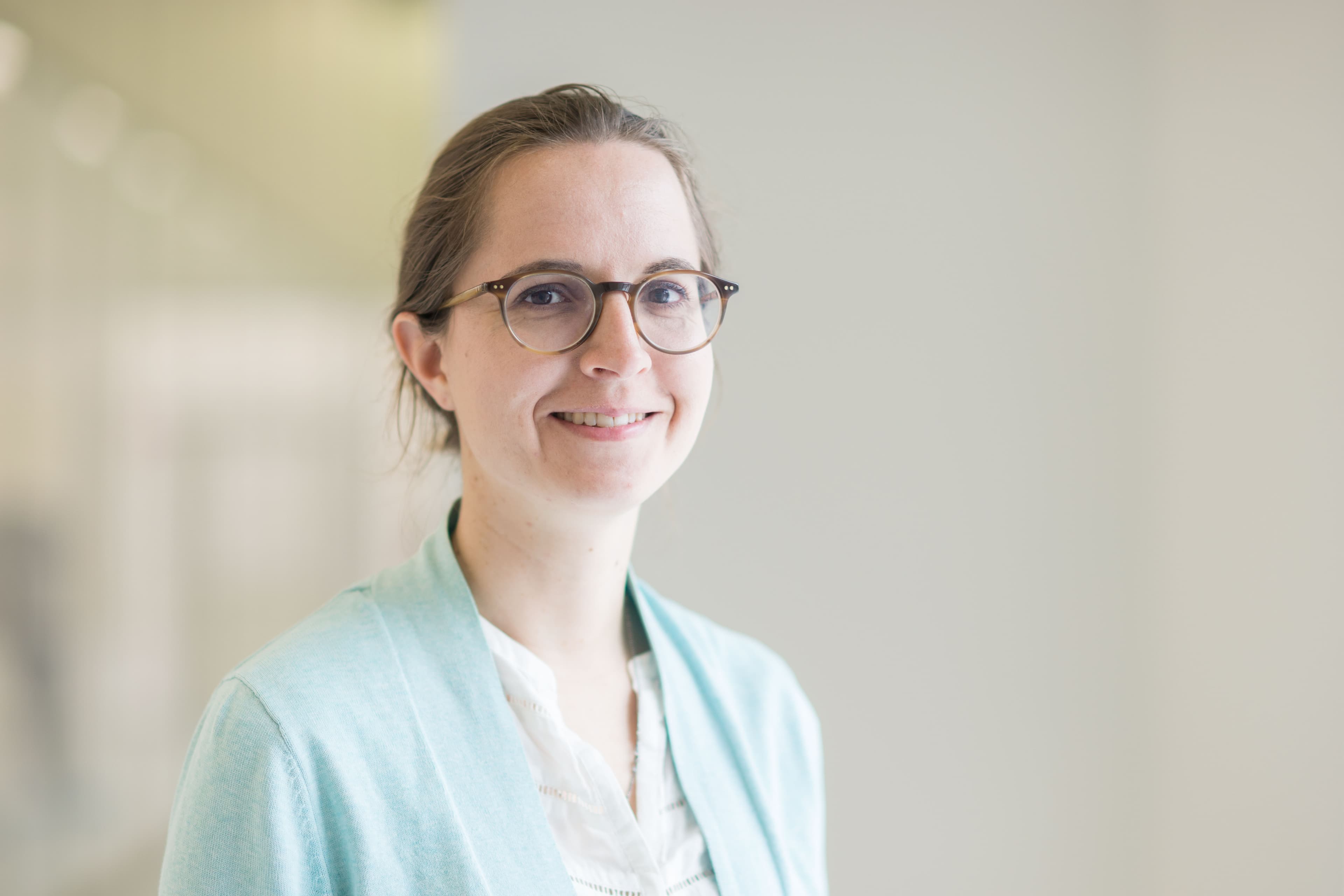
Dr. Eszter Voroshazi is the group leader of PV system activities at imec on the EnergyVille campus. This research group focuses on innovative PV-module and powerelectronic technologies and energy-yield simulations for integrated PV systems. She received her engineer certification from INSA de Rennes (2008) and her Ph.D. from KU Leuven(2012).
Kris Van de Voorde is the innovation program manager at imec. With a focus on clusters and transitions, he is initiating and supporting Industry 4.0 and circular-economy-related projects. He holds a master’s in electrical engineering (UGent), a third degree in industrial management (KU Leuven) and an MBA (Vlerick Business School).
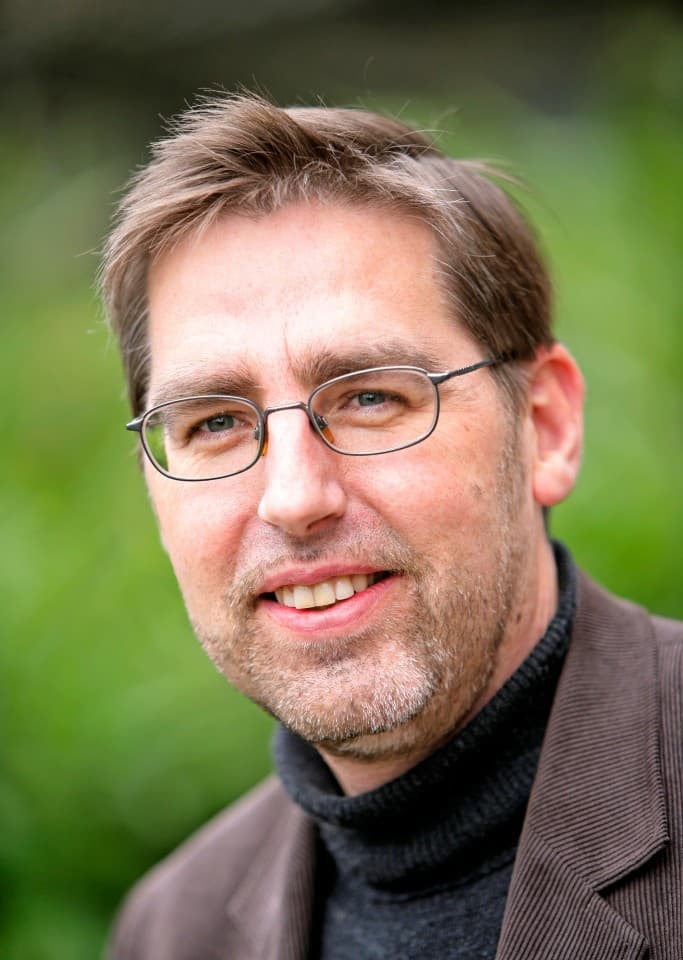
Dr. Jozef Poortmans is an imec Fellow and has been the scientific director of imec PV and energy activities since 2013. He is a part-time professor at KU Leuven and UHasselt, and is also the R&D strategy coordinator of EnergyVille, a partnership between imec, VITO, KU Leuven and UHasselt, which focuses on smart cities and smart grids.
Published on:
5 November 2018