The large number of sensors and actuators in industrial equipment or mainstream household devices is hard to ignore. Visual and touch interfaces are omnipresent on industrial equipment and all kinds of sensors that explain exactly what is going on inside the machinery. It’s a bit like the evolution of household printer troubleshooting, guiding you step by step whenever a sheet of paper gets stuck or alerting you when an ink cartridge needs replacement. Nowadays, even an electric toothbrush comes with OLED screen and Bluetooth connectivity. Imec has internally reorganized and upgraded its activities on sensor and actuator technologies to better cater to the evolving needs of this growing industry. A shift towards higher TRL levels in combination with more pro-active developments on specific applications are amongst the strategies, as Paul Heremans, vice president sensors and energy technologies at imec, explains.
Market trends
There have never been as many sensor and actuator devices in industrial and consumer devices as there are today. The industrial-sensors market exceeded $20B in 2019, according to a report by Global Market Insights. The demand in sectors such as manufacturing, energy and power, and healthcare will push global shipments of industrial sensors above three billion units by 2026. This is a staggering number, yet only half of what is seen in the imaging industry. IC Insights estimates image-sensor shipments to surpass six billion units in 2020 already. This might not come as a surprise, knowing there’s an average of more than three cameras in each smartphone nowadays.
The key to these immense growth numbers is the scalability of the sensor and actuator devices and their building blocks. Scalability in terms of ‘manufacturing capacity at acceptable cost’ and scalability often also in terms of ‘downscaling their form factor to fit into embedded or mobile devices.’ Take, for example, a high-end infrared camera. Depending on the desired specs, its current price point can go up to ten thousand euros, which puts it within reach of a limited number of application areas such as military and space. Once similar capabilities can be integrated at a fraction of the cost (and size), an explosion of new markets and use cases can happen in industries such as life sciences, security, instrumentation, agrofood. The current approach to use III-V materials and flip-chip assembly will not be sufficient to reach the necessary miniaturization and cost-efficient manufacturing goals. For this to happen, upscalable CMOS-based technology on 200 or 300mm wafers is an indispensable enabler.
Aside from these quantitative targets, the industry is also looking for new modalities and additional ways to integrate sensor and actuator solutions. For example, but not exclusively, to get certain applications within closer reach of a larger number of end-users. A prime example is Apple’s integration of a light-detection and ranging (LiDAR) scanner in the iPad Pro 11. Trends in mobile displays demonstrate the possibilities in a wide range of applications. OLED displays are becoming the dominant technology for mobile phones and watches. There is barely a need to further increase the resolution (~500ppi in the state of the art), but the trend is to make the display as large as the screen, i.e., remove all visible bezels. As a consequence, the sensors integrated into the front screen need to disappear from the display: ambient light sensor, proximity sensor, selfie camera, fingerprint sensor, face recognition, and heartbeat. Furthermore, we can expect more sensors to find their way into the display, e.g., an integrated 5G antenna or haptic feedback. And as the smartphone is becoming the prime personal assistant, there is a trend to integrate more health-monitoring sensors, such as an oxygen saturation sensor, glucose sensor, analyzer for allergens, etc. And this is ‘just’ about smartphones; we can depict similar scenarios for almost all other application areas as well.
Technology enablers
Imec’s focus is twofold: to enable miniaturization and to develop new sensor and actuator modalities, both by leveraging the available semiconductor expertise. As for new modalities, the development of a short-wave-infrared CMOS camera is an excellent example of a recent achievement. In 2019, imec demonstrated a camera-integrated solution allowing Si-based CMOS sensors to detect short-wave infrared wavelengths that are typically out of reach for them because of physical and optical laws. Scale-down was shown at IEDM 2020. Thanks to imec’s approach and expertise, such short-wave-infrared cameras can soon be made in high volumes at a much-reduced cost compared to today.
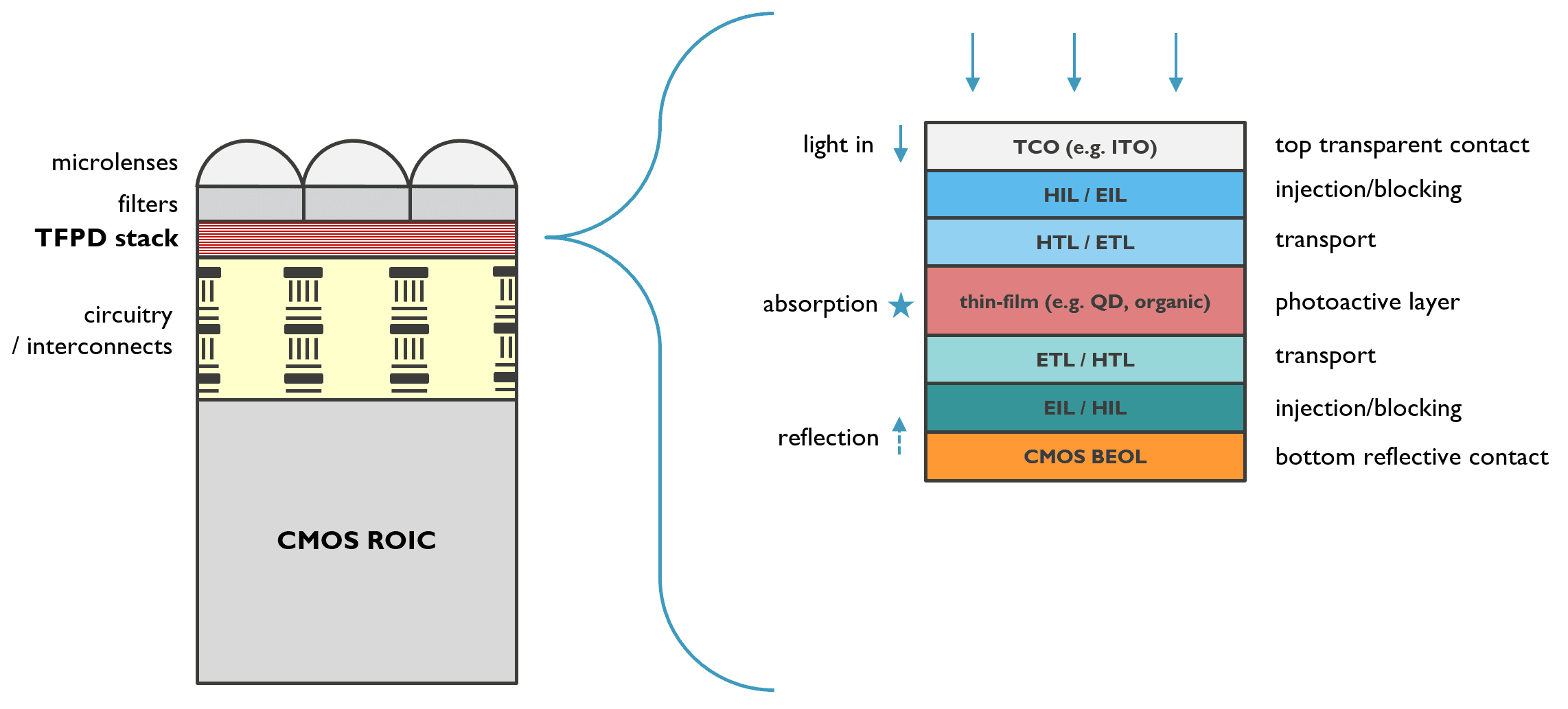
By processing a thin-film multilayer stack with photoactive layer sensitive in the infrared range (right), on top of a Silicon readout circuitry (ROIC), imec created an IR-sensitive CMOS imager (left) compatible with mass manufacturing.
Another example is imec’s work on photo-acoustic imaging. In photo-acoustic sensing, a light source sends radiation of a specific wavelength into a sample, where absorption causes thermal expansion. This results in sound waves that can be picked up by a sensitive microphone. Photo-acoustic systems have a benchtop-size today and are extraordinarily sensitive. For instance, they allow the non-invasive measurement of blood glucose levels, or the concentration of analytes in other contexts, with extreme precision. By using semiconductor technologies, imec aims to integrate ultra-sensitive microphones and light sources with high spectral purity onto a chip, bringing photo-acoustic sensing to the next level.
On a somewhat related topic, imec is also using acoustics, ultrasound in this case, for haptic-feedback systems. Haptic feedback is an emerging human-machine interface in which a machine can ‘touch’ its operator by triggering mechanoreceptors in the human skin without physical contact. This adds a new dimension of ‘touchlessness’ to currently available user interfaces and can play a critical role in the low-touch economy expected to emerge post-COVID-19. At the heart of the first generation of haptic-based interfaces are bulky piezoelectric ultrasound transducers, which are cumbersome to use, impede a very fine interaction, and limit end-product integration possibilities. Imec’s ambition is to develop a dense array of ultrasound transducers types in large-area format to modulate the output power and precisely focus the ultrasound beam in mid-air at distances ranging from a few centimeters to tens of centimeters.
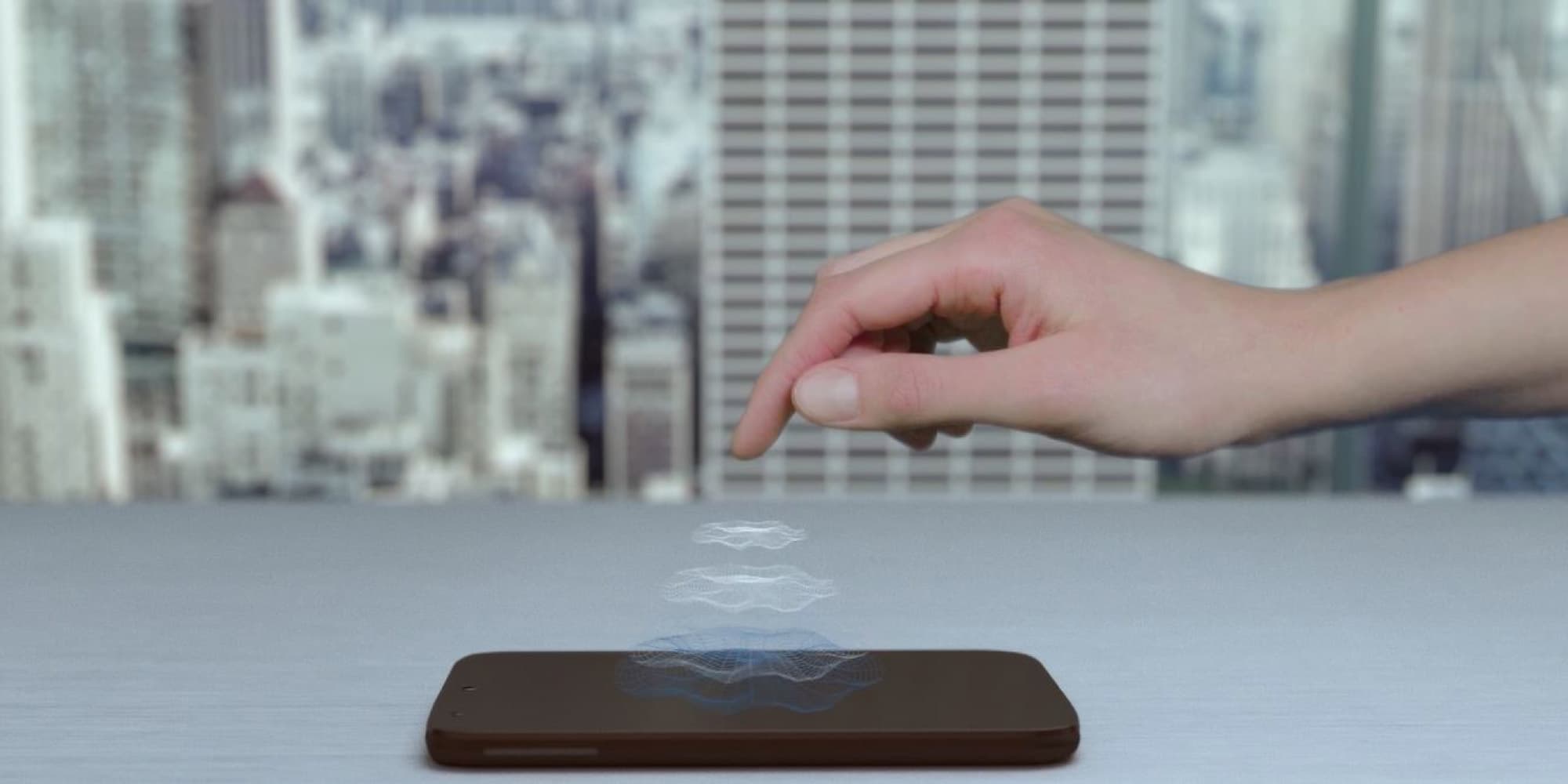
Imec develops integrated touchless interfaces based on ultrasound-based haptic feedback.
Imec technology moves up the TRL ladder
Through these examples, it becomes apparent that compatibility with semiconductor manufacturing always inherently enables scalability and often goes hand in hand with miniaturization and improved performance. Looking at the traditional building blocks of an electrical system (processing, memory, connectivity, input/output), imec is world-leading in each of them and now reinforces its focus on the sensor and actuator technologies that enable the system input and output.
The new strategy builds on two main foundations. It is more proactive in the technology development for high-potential application areas and takes these selected technologies towards a higher technology readiness level. Until now, imec was in its sensor and actuator developments, mainly focusing on its underlying capabilities (e.g., ultra-low-power electronics, thin-film technologies, imagers, microfluidics) and generic integration capabilities. In the new strategy, imec will strengthen its capabilities and be more proactive in developing prototypes and system demonstrators based on its own knowledge and insights into what these promising markets might need.
Two promising domains could undoubtedly be life sciences and industrial equipment. For both, there are numerous potential applications for sensor and actuator technologies, and they are close to imec’s application-oriented R&D divisions. In life sciences, there are many optical and acoustics-based system enhancements for diagnostics and surgery, and imec can create leverage via its life-science technologies division. Additionally, the entire industry 4.0 vision relies on sensor and actuator enabled solutions and can internally build on imec’s unique ecosystem of equipment suppliers. Other sectors will also be investigated. For example, agrofood, the focus area of imec’s OnePlanet initiative, could benefit from e.g., integrating SWIR cameras on drones for crop monitoring or using ultrasound technology to monitor fruit ripening. And in waste management, short-wave infrared or other electromagnetic waves can be used to sort plastics that are difficult or impossible to distinguish in visible light. And as soon as imec’s sensor and actuator engine is oiled and running in these business-to-business sectors, it won’t shy away from consumer-electronics domains either.
Want to know more?
-
Read the recent press release on imec’s miniaturized SWIR camera as presented at IEDM2020: Imec Presents a Thin-Film Short-Wave-InfraRed Image Sensor with Sub-2µm Pixel Pitch | imec (imec-int.com)
-
Learn how imec brings photolithography into the domain of OLED manufacturing in the IDW2020 press release: Imec Applies Photolithography To Push Functionality and Reliability Barriers In OLED Display Manufacturing | imec (imec-int.com).
-
Read all about imec’s SWIR-enabled CMOS camera in the imec magazine article “Make smartphones and autonomous vehicles see the impossible.”
-
Read the imec-magazine article and watch the video on “Haptic feedback: the next step in smart interfacing.”
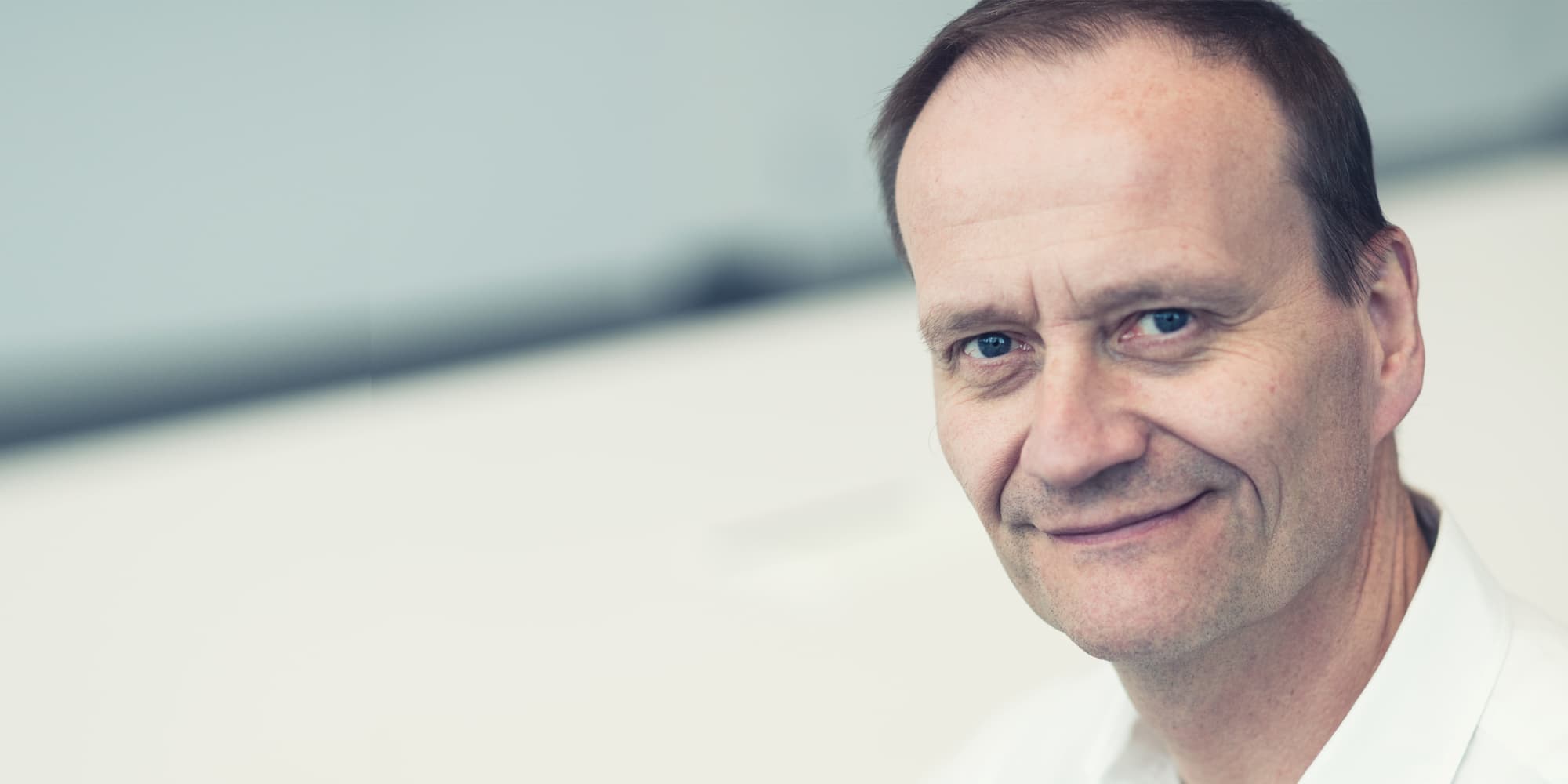
Paul L. Heremans is the vice president of sensors and energy technologies and a senior fellow at imec. He is also a Professor at the University of Leuven in the EE department (ESAT). Paul received his PhD in Electrical Engineering from the University of Leuven, Belgium, in 1990. He then joined the opto-electronics group at imec, to work on optical inter-chip interconnects, and on high-efficiency III-V thin-film surface-textured light-emitting diodes. In 1998, he started the thin-film electronics activities at imec.
Published on:
10 December 2020