On January 28, a Soyuz rocket successfully launched the HISPASAT36W-1 satellite from the European Space Agency’s launching site in Kourou, French Guyana. The HISPASAT36W-1 is an innovative communications satellite to be positioned in a geostationary orbit, 35,786 kilometers above the Earth's surface at a position of 36 degrees West. Once in place, it will provide relay coverage and multimedia services across Europe, the Canary Islands and South America at the service of Hispasat, a world leader in Spanish and Portuguese broadcasting. The satellite’s electronics contain an impressive 645 chips to which imec has contributed. “And it is the first flight mission of chips designed with imec’s DARE (Design Against Radiation Effects) platform,” explains Steven Redant, ASIC Design Services Manager at IC-Link, imec's industrial service for innovative chip design and fabrication.
The Hispasat36W-1 satellite is the first to use SmallGEO, the Small European Geostationary Platform developed under the ARTES program of the European Space Agency (ESA). With SmallGEO, the satellite’s German manufacturer OHB hopes to produce its next satellites faster, at lower cost, and with a great flexibility. SmallGEO is highly modular, and satellites based on it can be fitted to the customer’s requirements without major modifications to the design and with various types of payloads, e.g. for telecom but also for earth observation. Also, future SmallGEO satellites will be able to use full electric propulsion to get into orbit. This will substantially reduce their weight, as they no longer need to carry additional compressed gas.
The payload of Hispasat36W-1is the RedSAT telecommunication system commissioned by Hispasat and developed in collaboration with ESA by a Spanish consortium.
“Compared to conventional telecom systems in satellites, RedSAT makes a much more agile and efficient use of the on-board power and bandwidth,” says Steven Redant. “This improves the service to end-users because they can do with smaller terminals and can have communication among users in a single satellite hop. Moreover, RedSAT slashes the conventional satellite signal delay - or latency - by half, which greatly boosts real-time applications such as videoconferencing. All this thanks to RedSAT’s on-board signal regeneration and its active antenna.”
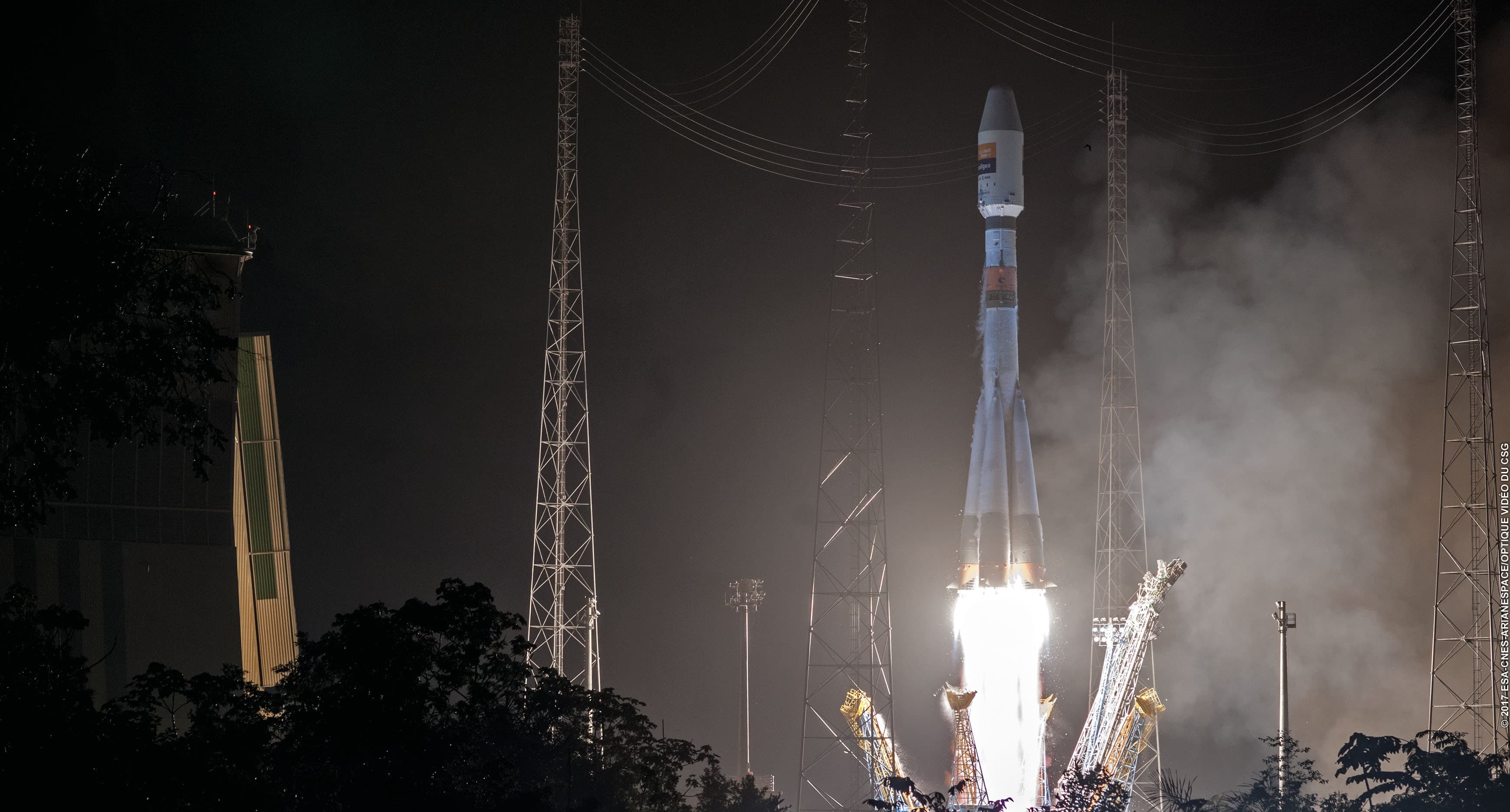
Launch of Hispasat 36W-1 (image: ESA/CNES/ARIANESPACE)
Improving transmissions in space
In traditional telecom satellites, the incoming signals are basically echoed: they are transmitted unchanged and always at the same power, irrespective of, e.g., the available channel or the weather conditions. But this consumes too much energy under all but the worst-case conditions. Moreover, errors in the uplink signal are resent and compounded with additional downlink errors.
Not so in the Hispasat36W-1 satellite, which uses a so-called ‘regenerative technology’ that adapts the signal power to the circumstances and corrects uplink errors before retransmitting the signal. This allows the satellite to operate at a lower power budget and transmit a signal that needs fewer error-correction coding, which improves the satellite’s throughput. In addition, the available on-board computation simplifies the ground station processing. The result is a much simpler network, optimizing the size and power of the user terminals and simplifying links that would normally require a double hop, thereby reducing signal latency and providing better real-time services.
To pull this off, the satellite contains 23 transponders, 20 in the Ku band and 3 in the Ka band, two microwave bands used for satellite communication. These receive signals from satellite ground stations, regenerate them, and transmit them on the downlink frequencies to receivers on Earth.
Steven Redant: “At their heart, these transponders contain the Knut chip. Knut is a radiation-hardened mixed-signal ASIC that carries out pulse width modulation for the transponder’s traveling wave tube amplifiers, specialized vacuum tubes used to amplify microwave signals. Knut was commissioned by TESAT Spacecom (market leader in telecom payloads for satellites), financed with the help of DLR (the German Aerospace Center), and, for all but the digital functional description, designed, fabricated and qualified through IC-Link.”
“We provided the digital cell libraries to radiation-harden the digital part of the chip: our DARE libraries for the UMC .18um technology. But apart from that, we also designed the analog blocks, synthesized the chip and made its layout. And we managed and oversaw the chip manufacturing at UMC and the full flight model lot qualification. With this launch, we are at TRL 9 (Technology Readiness Level) for our DARE UMC .18 platform. It means we have shown to companies and institutions in need of radiation hardened chips that IC-Link has the knowledge, flexibility and solutions to assist them in all stages of their chip realization.”
Steering the active antenna
The second major difference with comparable communication systems is RedSAT’s antenna, nicknamed ELSA (ELectronically Steerable Antenna). It’s the first such active antenna for a commercial communications satellite.
An active antenna is an array of smaller physical antennas that together create a directed beam of radio waves, a beam that can be electronically steered to point in different directions without physical movement. It does so by feeding the radio signals to each individual antenna adding a computed phase shift. The result is that the emitted waves from the separate antennas add together to increase the radiation in a desired direction, while they cancel each other to suppress radiation in undesired directions.
ELSA is managed by a number of hybrid electronic modules, each containing four analog and twenty digital ASICs. In total, the antenna has 622 chips, 102 analog and 520 digital.
Steven Redant: “The use of such a large quantity of ASICs in a single mission is a remarkable technological milestone. A milestone to which imec contributed by assisting in the realization of both antenna chips, which were commissioned by Arquimea, the Spanish electronics integrator for its end-customer Airbus.”
“The analog ASIC was implemented in a 0.35um technology of On Semiconductor (Belgium). It is a high-voltage chip, for which we provided technology and hardening advice, did a design review and managed the manufacturing. Arquimea designed and qualified the chips, which then were mounted into hybrid modules by Airbus. The second, digital ASIC, also designed by ARQUIMEA, was fabricated in the 0.18um UMC technology, again using imec’s DARE radiation-resistant digital cell libraries. Here, we’ve also done the layout and adapted the IOs to the requirements of the hybrid module. Such flexibility is an important asset in our offer.”
What’s with imec and radiation-hardened electronics?
Chips used in spacecraft, airplanes and also e.g. in high-energy physics experiments are prone to failure or intermittent errors caused by effects of radiation in the environment where they operate. To be hardened against these failures and errors, they have to be designed in a specific, nonstandard way.
“But here’s the catch,” says Steven Redant. “Chips for space applications are not produced in the volumes that are commercially interesting for foundries. Therefore, many foundries that used to have technologies specifically for radiation-hard ASICs have left the market. To provide a high quality alternative, we developed the Design Against Radiation Effects platform, with the support of ESA. DARE is a combination of digital cell libraries, methodology support for analog design and the re-use of previously designed analog IP blocks. With DARE, we have the basis to design competitive, high-performance, low-power solutions for non-military applications that will operate in environments with harsh radiation.”
“In addition to using the available building blocks, our experts can develop custom-defined and application-specific blocks, all with the proven DARE hardening techniques. And we can also port the hardening concepts to other technologies and nodes. Examples that we’re currently focusing on are XFAB .18 XH technology for space projects and building blocks in TSMC technologies for use in high-energy physics experiments. We have also built an analog DARE environment for On Semiconductor’s I3T80 process, and we have started DARE activities in 65nm TSMC technology.”
Designing chips is one thing, being able to help customers wherever they lack expertise is another one altogether. IC-Link has made it into its hallmark to provide customers with specialized expertise on the path from idea to electronic application. This includes among others selecting the appropriate technology, designing and reviewing designs, prototyping, but also providing access to the world’s most advanced foundries for volume production.
Steven Redant: “And as we’ve demonstrated with the Knut chips, we have extensive experience in the field of space evaluation (ESCC2269000) and qualification (ESCC9000). This includes developing and customizing the hardware required for screening the flight modules, such as test load boards, packages and sockets as well as managing the whole supply chain.”
Want to know more?

Steven Redant joined imec in 1989 as an application specific integrated circuit (ASIC) design engineer. He designed ASICs for, amongst others, space and medical applications, taught the use of VHDL as a design and verification language and was involved in the radiation-hardening-by-design proof-of-concept until in 2000 he became group leader of the design team. He has led the path of concept to the current DARE platform offer. His design team also provides chip design services for imec scientific demonstrators as well as for industrial applications.
Published on:
5 March 2017