Composites: much used, but hard to understand
Composites are extremely strong and light materials because they are a combination of polymers, and glass or carbon fibers (which give the material greater strength). Composites are used in a whole range of applications: in aircraft (for example in the mechanics of the wing flaps and in fact in 40% of all of the aircraft’s components), as the base material for carbon-framed bikes, in Formula 1 racing cars (about 85% of a Formula I car is made from composite material), for the blades on wind turbines, in pressure vessels for storing gas, in prostheses, boats, electric cars – and so much more. Space flight is starting to show a growing interest in composites, too.
A composite is what is called an ‘anisotropic’ material. This means that the material’s mechanical properties are not the same in all directions. This is explained by the material’s complex composition. And it is this very anisotropy that makes it difficult to predict when a part of an aircraft, car or wind turbine made from composite materials will break.
It is for this reason that simulations are made of these structures. For this to happen, data from sensors is required, showing the ‘real’ measurements in the material. In order to obtain that data and to keep track of the actual status of the components in real-time, sensors are used – usually optical fiber sensors. The disadvantage of these sensors is that they mainly measure stress along the length of the fiber. However, an overall picture of the material’s ‘health status’ can be gained by placing the fiber sensors in different directions on the composite material. But placing the sensors in exactly the right place is very time-consuming and difficult.
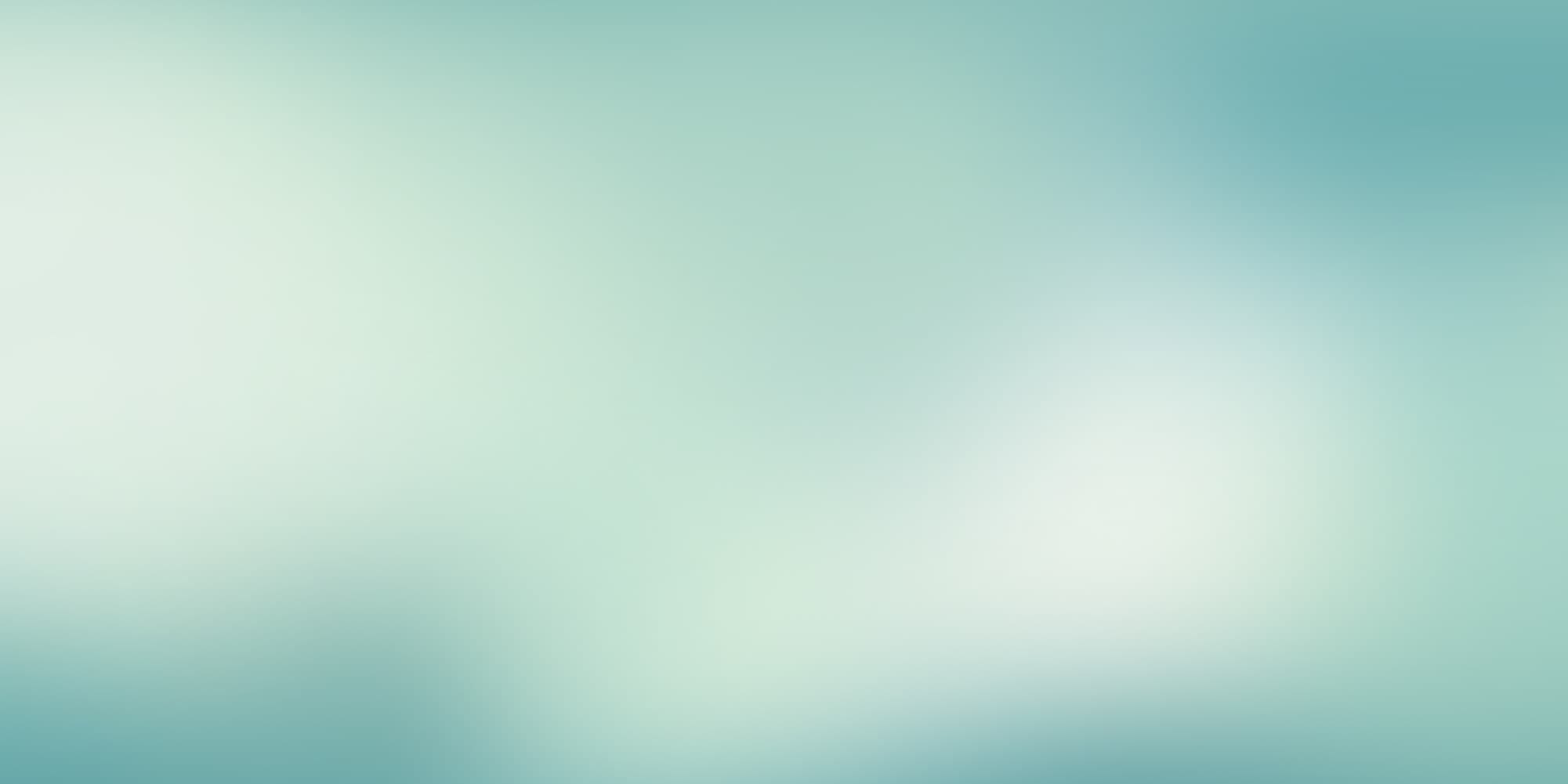
New research is now making it possible to incorporate very thin sensor foils – with optical sensors placed in various, precisely defined directions – into composite materials during the production process.
Sensor foils with light
CMST, imec’s research group at Ghent University, specializes in developing foils with electronic components that are used in applications such as smart clothing. Photonic components – which pass on or measure data based on light – can also be integrated into foils. ‘Flexible photonics’ are still in their infancy compared with flexible electronics. This is because it is still a fairly complex business aligning the photonic components in a foil in such a way that they can engage and disengage the light properly.
The new foil for measuring stress in composite materials contains three optical ‘gratings’ that are positioned at angles of 45 or 60° to each other.
Light with a certain wavelength is reflected by these structures. In case of strain, this wavelength will change and this change can be detected. Combining the measurements of the three gratings makes it possible to calculate the stress across the whole surface. The foil is extremely robust and can be curved to a curvature radius of 11 mm and elongated by 1.4% without losing functionality. In all likelihood, the foil can be stretched even further, but thus far it has only been tested to 1.4%.
Because composite materials are produced at relatively low temperatures – at a maximum of around 150 to 200°C – sensors can be incorporated into them without damage. This also appears possible in the case of sensor foils with optical gratings. Three different mechanical structures have been produced as a demonstration: hinge arm, a control arm and a panel.
Sensor foils making safer bicycles, aircraft and pressure vessels
Cleverly, the foils can be used to measure the ‘health’ of a composite while it is actually being used. So bicycles, aircraft and pressure vessels will be able themselves to report when there is a problem or if a part needs replacing. This means that pictures of wind turbines with ‘hanging’ blades will become a thing of the past (as will damage to the turbine itself).
The foils will also eliminate the need for excessive maintenance and parts will only be replaced when it’s really necessary. All of which will push down maintenance costs and reduce material usage. And – even more important – maintenance providers and users can be timely alerted in case of a problem with the composite material. That way, accidents can be prevented.
Cheaper production of composites thanks to sensor foil
A sensor foil – with photonic and / or capacitive sensors – is of value to research departments in companies that produce composites.
The process itself can be optimized by incorporating the foil into the composite and then taking readings during the manufacturing process. For instance, capacitive sensors have already been used in foils to determine exactly how long the curing phase has to be. The shorter this phase, the less expensive the process. The foil itself is so thin that it has no effect on the manufacturing process.
What about other materials and applications?
Foils can also be used stand-alone, applied to things such as metal surfaces. Not only are foils able to measure strain, but vibrations as well. In actual fact, vibrations are a form of (dynamic) strain. And what do you think about measuring gases in food packaging? Sounds like a good idea – but that’s still something for tomorrow! In the meantime, spectacular progress has already been made in the short term, so that a carbon-framed bike can tell the rider when the situation is becoming dangerous or a pressure vessel is able to set off an alarm to say that the pressure is rising dangerously high.
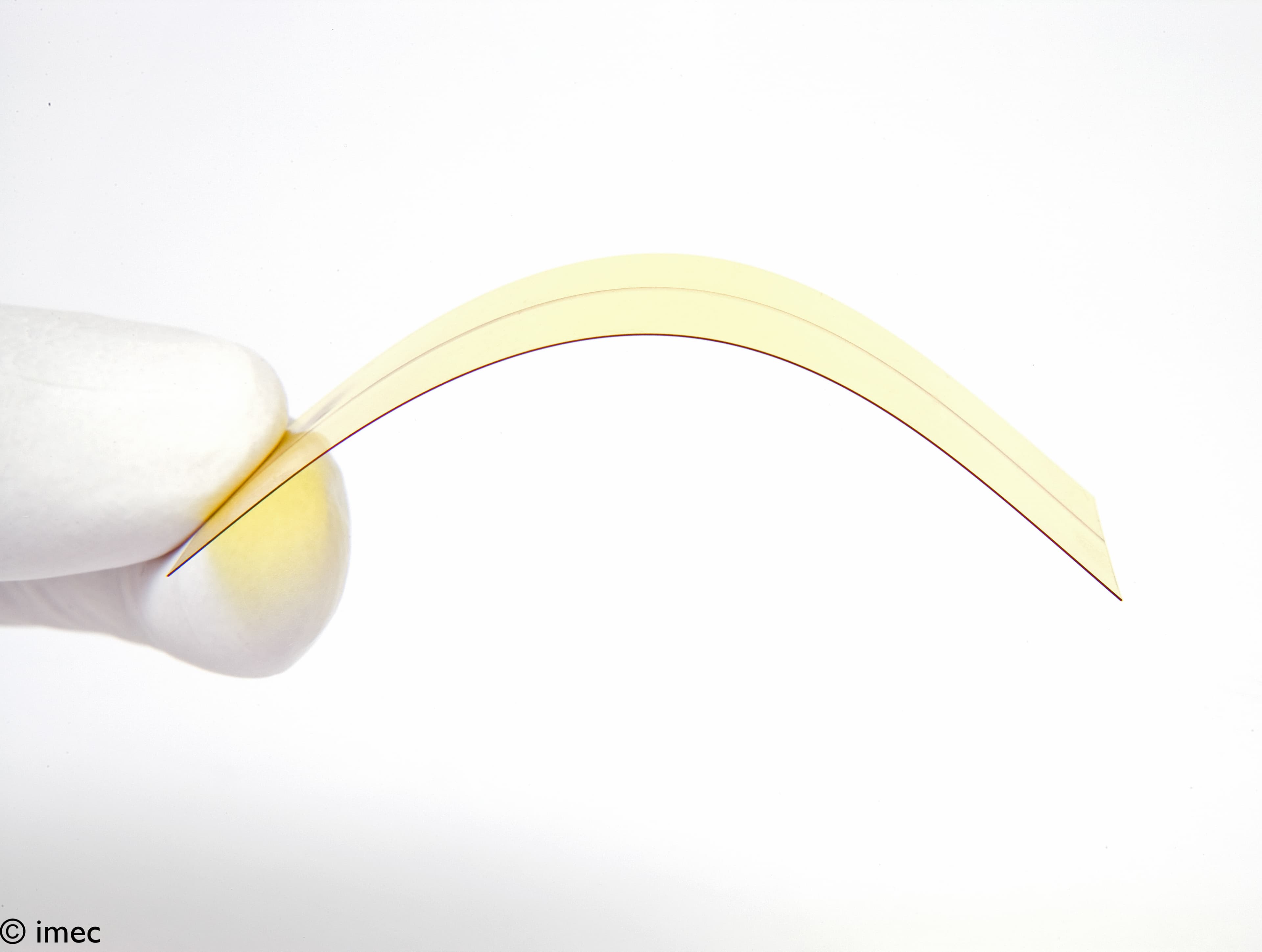
Foil with photonic waveguides
Want to know more?
- Use our contact form to request the paper on “Thin and flexible polymer photonic sensor foils for monitoring composite structures”.
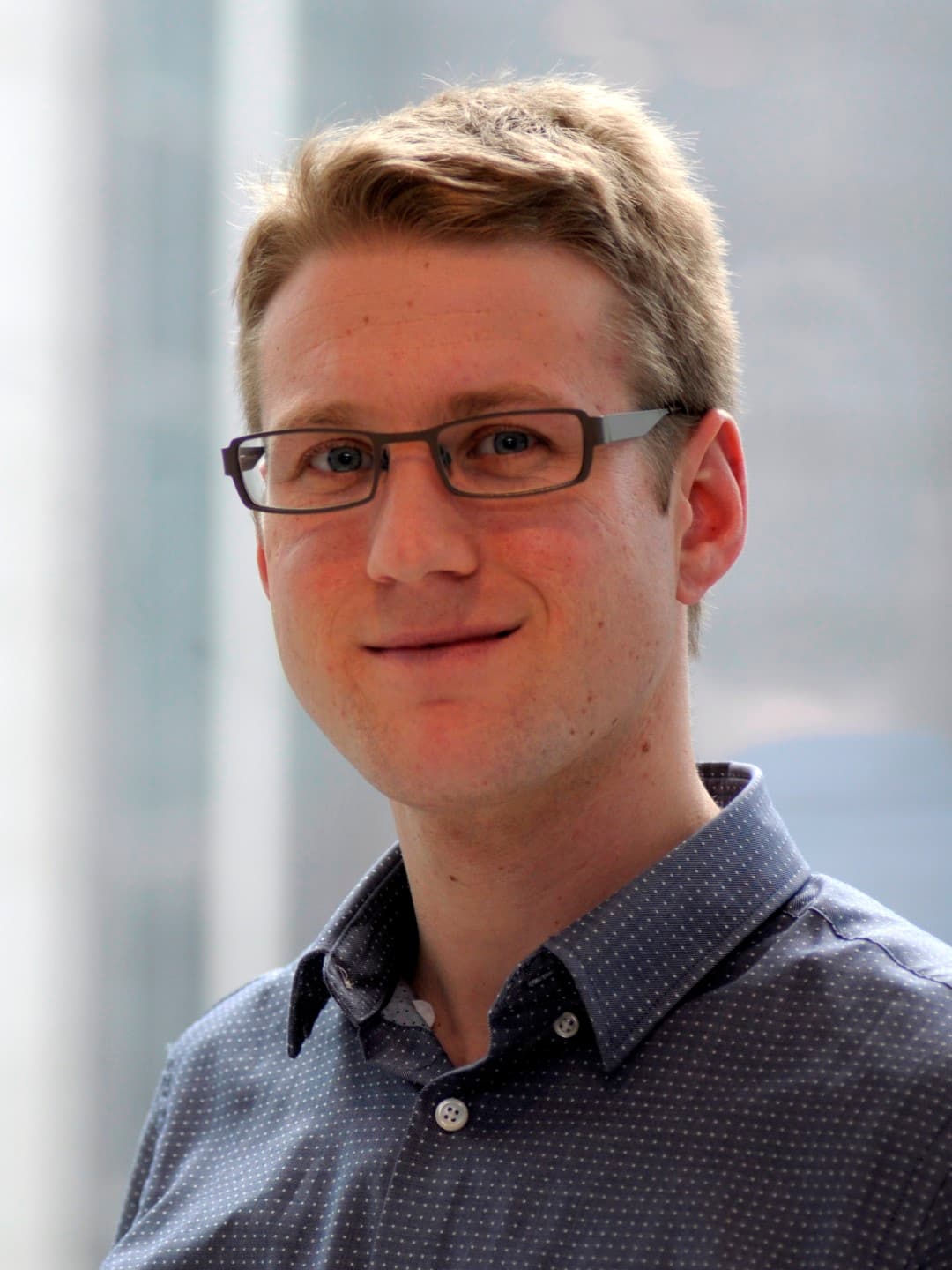
Jeroen Missinne was awarded his Master of Science degree in Electrical Engineering in 2007 and his PhD in Electrical Engineering in 2011, both at Ghent University, Belgium. He is currently employed as part-time professor at Ghent University and employed at CMST (Center for MicroSystems Technology), an imec research lab at Ghent University. He has expertise in optical sensors (strain, pressure, (bio)chemical sensing) and photonics packaging technologies (integration of sources and detectors, polymer and laser-written glass waveguides, etc.). Jeroen Missinne has authored or coauthored more than 40 publications in SCI-stated journal papers and international conferences. He is the co-inventor in 5 patents or patent applications.
Published on:
27 April 2018